Insight
Virtual Brewery: Simulation can prevent problems and add value to brewing sector
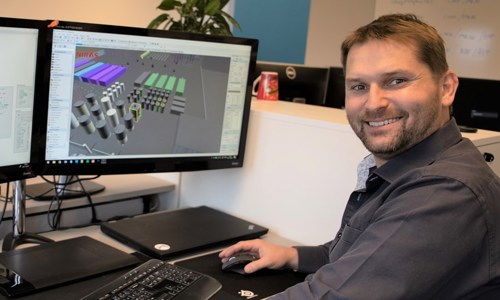
Insight
Digital simulation programs in the food and beverage sector have improved immensely in recent years. NIRAS’ expert knowledge of how to combine these tools with process design can contribute to decrease construction costs, prevent bottlenecks and add overall value to breweries.
When a brewing company starts construction on a new brewery or wants to upgrade an existing production site, the decisions that are made during the design phase are crucial for the future operation of the plant. Correcting errors at a later stage can be highly costly. Consequently, all decisions should be based on the best possible knowledge.
In this regard, it is important to be able to foresee and solve any potential problems as early as possible. To this end, NIRAS offers a highly specialized simulation software that can build precise and predictive models of breweries in order to ensure that our clients make informed decisions.
A simulation model is a computer imitation of the operations of the actual plant, which can be built in the early design phase. Simulation can be a highly cost effective way of anticipating and avoiding potential problems in connection with the design of new brewery or beverage production facilities.
Obviously, one of the major concerns when making a new brewery is to guarantee a smooth and unproblematic production and to avoid any potential delays. In this context, simulation is also a practice that can solve bottleneck issues in existing facilities or in connection with plant upgrades.
"Once a simulation model has been built, verified and used to optimize the plant design, the same model can be used again during the ramp-up / commissioning phase and also during regular production planning at the plant."
Christian Wordenskjold Nørregaard, Simulation Specialist
Likewise, simulation technology can also support production planning in case of high complexity of end product and raw material flow.
Even while the design of a plant is developing, the simulation model can be continuously updated which means that the client is able to make decisions based on the latest available and best possible data.
However, if for instance a brewery does not fulfill all these above mentioned factors, then a simulation model will most likely add value. As a minimum, it will provide validation of your plant design and the robustness of the design to cope with equipment failures and variations in demand, product mix, quality issues etc
To illustrate how NIRAS’ simulation tools can add value to the brewing sector, we can have a look at a previous NIRAS simulation project.
NIRAS was asked to validate the design of a new multi-story production plant in Europe. The plant had been designed based on spreadsheet calculations, which is the normal methodology. However, there were some complexities. Some of the production processes had a natural variation in process time, the load on the different steps of production process was quite different depending on the product and, finally, what manning level was required.
We obtained all available information from building drawings, equipment drawings, equipment specifications, production plans, product recipes, process times, and manning requirements to operating procedures. Operating procedures were not completely documented, so we developed a structured production management model, which is essential to be able to build a well-structured simulation model.
Once all the information was available, the 3D discrete event simulation model was built. Upon model verification, the model was ready to test the design. The simulation model immediately identified a major bottleneck was identified and solved. Next, surplus capacity was identified. By running a number of different configurations of equipment and manning, the optimal configuration was found.
All together the simulation model reduced the equipment investment by € 630,000 and 120m2 floor space. The cost of the simulation model was € 60,000. So in this case the simulations added a considerable value, compared to its cost. However, unlike a design project, it is not possible to anticipate if equipment savings or bottlenecks will be found.
But if simulation does not necessarily guarantee added value, is investing in it like buying a lottery ticket? This depends on series of factor, such as:
If everything at your production facility runs smoothly; if all your processes are very stable; if you do not have inter-dependencies; if making the optimal schedule is straight forward; if everyone fully understands the process; if operator work situations are well designed and pre-training is not an issue; if the product mix does not change throughout the year; if new products are very similar to the current product; if equipment is stable; if raw material suppliers are reliable, and if the raw materials are in excellent quality – well, then a simulation model in most cases will not add value.
"Based on numerous real-life cases, the use of a simulation model could prove highly beneficial."
Christian Wordenskjold Nørregaard, Simulation Specialist
However, if for instance a brewery does not fulfill all these above mentioned factors, then a simulation model will most likely add value. As a minimum, it will provide validation of your plant design and the robustness of the design to cope with equipment failures and variations in demand, product mix, quality issues etc
One of the benefits of a simulation model is that it not a one-off. Once a simulation model has been built, verified and used to optimize the plant design, the same model can be used again during the ramp-up/commissioning phase and also during regular production planning at the plant.
During the commissioning phase, the simulation model can be loaded with the current performance, current inventory and the expected ramp-up curves of a food and beverage plant.
This will help in creating realistic production schedules, planning manning requirements and anticipate production output and problems, thus enabling mitigating actions before problems occur.
During regular production at a brewery or other food and beverage plants, the simulation can be used to predict the future production and help making production schedules. By integrating the simulation model with the plant MES/SCADA/PLC system and IoT devices, a digital twin is born.
Consequently, a real time virtual factory is available. So a single model can be used to predict future production, predict impact of changes to equipment, predict impact of new products, etc.
In NIRAS we have used our simulation tools in a wide range of traditional manufacturing such as biotech, food, breweries and warehouses.
But we have also used it to make simulations of automated underground parking facilities, sterile hospital equipment process plants, automated hospital logistics, clinical hospital processes, mixed road construction traffic and people flow in buildings with elevators.
And based on numerous real-life cases, the use of a simulation model could prove highly beneficial.
NIRAS is among the most experienced logistics consultancies in Denmark, and the company has created optimal logistics solutions for some of the biggest hospitals, breweries, dairies, and industrial production companies in Scandinavia and world-wide.
Recent NIRAS simulations projects include: